Protecting Your Building – Replacing Sealants and Coatings
As managers and owners move forward on building maintenance and capital improvement initiatives planned for the next year, one of the most important and necessary projects many will pursue is the replacement of worn, cracking or peeling sealants and coatings to ensure the continued integrity of building exteriors. While this may appear to be a relatively straightforward endeavor, it is important to take steps to ensure the job is done right the first time or you may have to repeat this costly process sooner than expected.
What are Sealants and Coatings?
Sealants (or caulking) are the materials used to prevent damaging moisture ingress around perimeter areas such as windows, doors, frames, glazing and expansion joints. Typically, sealants need replacement every 7-15 years, depending upon the materials used.
Coatings are finishes that repel wind, rain, dirt, mold and mildew in order to protect a building’s concrete exterior from erosion. Unprotected concrete allows water intrusion which corrodes the embedded steel – causing breaks and other damage to the concrete. This type of damage is expensive to repair, but can be avoided with the application and maintenance of appropriate coatings. Acrylic-based coatings can last from 7-10 years, while more costly silicone-based coatings can remain true for over 10 years before recoating is necessary.
The Right Approach to Protect Your Investment
The following steps will help ensure that your replacement sealant and coating project delivers effective and long-lasting results:
- Evaluation. A qualified professional should review existing reports and construction documents and perform a visual examination of the materials currently in place to determine their makeup and condition. Are the materials cracked? Are they peeling? Are they stained?
- Adhesion and Product Compatibility. It is important to consult with the manufacturers of the proposed products to gain their opinion and guidance relative to which compatible replacement materials are most likely to deliver maximum adhesion and life expectancy. Preliminary testing should be performed to verify the recommendations. Basically, you want to make sure that the new materials will adhere to what’s currently in place AND that what’s currently in place is well adhered. If not, both old and new materials will quickly begin to pull away from the building.
- Product Specification and Application Oversight. Once the right products are determined, specifications are developed for their application. At the onset of construction, additional compatibility testing should take place to re-verify the preliminary analysis and confirm the appropriateness of the materials to be used and their adhesion levels. This pre-construction testing will also unveil any potential compatibility issues between the sealant and the coating. A final field test performed during construction will ensure that application levels are within the acceptable range of the manufacturer.
An experienced structural engineering professional can help you evaluate the current status of your building’s sealants and coatings. If replacement is necessary, the SE can guide you and your building management team through these steps and provide a bid list of qualified construction companies. These organizations have proven themselves to be capable of meeting project requirements and quality expectations.
K2N Crest specializes in creative problem solving in the practices of architectural design, structural engineering, architectural engineering, interior renovation, forensic engineering and roof consulting. Building owners and managers throughout Illinois and contiguous states and Hawaii look to K2N for their architectural, structural and roof evaluation needs. For more information visit www.k2n.com or call us at 630-990-9595.
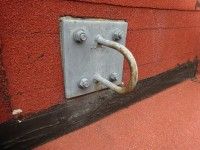
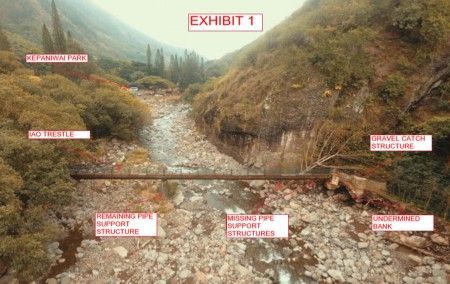